With many NSX owners purchasing cheap knock off Quick Release (QR) / hubs, I thought I should share some info on where these cheap knock offs came from. Not many people realize that many of these replicas are simply reverse engineered products of Works Bell, who developed this system.
HOW THE GENUINE WORKS BELL RAPFIX II IS MANUFACTURED
It is not widely known, but Works Bell actually invented the Ball Lock Quick Release Locking System as seen in the Works Bell Rapfix II (and unfortunately also seen in numerous copies). Works Bell also holds the patent on this system. If you go to the press release on their website you will see comments from the CEO of Works Bell, Mr. Masato Miyashita on this point. It reads ..."CEO of Works Bell, Mr. Masato Miyashita said of the new business relationship with The Tuners Group ..."Works Bell has been manufacturing and selling steering hubs since 1971 and we have provided the steering hubs for a lot of Japanese manufacturers and companies. We developed the 12 Hole PCD steering hub which can be used both for Momo steering wheels and Nardi steering wheels in 1977. Furthermore, we also took the patent for this product. From then on, we have never failed in technology, quality and durability of our products. We are the number one manufacturer in Japan today. We have also received some patents for our other products and we research, develop and innovate on new products every day. We developed and received the patent on the Quick Release (Rapfix Ball Lock System) in 2001. We have produced and sold 30,000 Quick Release Rapfix systems to date. " The Works Bell Rapfix II Plug and Socket start out as billets of high strength A5056 alloy.This high strength A5056 Alloy is then heat treated to H34 standard which increases the yield strength of the metal by 60%, to approach that of Duralumin, widely known as a super strong material. Works Bell don't stop there though ...This high strength and heat treated A5056 Alloy is then cold die forged. Die forging is the same process used in the manufacturer of ultra high grade alloy wheels and is mentioned in our tech article about forging vs casting vs machining. Here are some diagrams of a metal part (shown in red) being made using open die forging ...
This die forging process process produces a forged blank that is close to the final shape of the Rapfix II. The die forging makes the metal ever more dense, and aligns the grain structure matrix with the forging flow lines. Here is a diagram of that process ...
Forging aligns the grains of the metal like this ...
Here's a close up photo of the grain structure of a Rapfix after forging. The red lines show the flow of the grain structure after forging.
Here is a photo of the two main parts of a Rapfix II after forging and before machining
Next is the machining. Only now is the machining done, and because the grain structure is already aligned with the shape of the part via the cold die forging, the machining does not "cut across" the grain structure like the example shown in our tech article about machining non-forged metals.
The main body of the Rapfix is machined ...
Next an Alumite oxide film is caused to form on the surface of the aluminium and stainless steel by soaking the parts in an electrolytic liquid solution and changing the temperature to produce a surface with superior corrosion and wear properties.This produces a hard alumite oxide film, that is harder than steel. Alumite performs beautifully on the exterior while reducing any wear from use ...
On the black version of the Rapfix II, Works Bell use a special treatment called hard almite to effect a black sleeve ...
On the Rapfix II the inside sleeve where the socket and plug slide is then treated with a special teflon coating to make it much more difficult to scratch the anodizing ...
So now the Rapfix II is ready for assembly ... As you can imagine, Works Bell don't scrimp on quality here either. SUS304 stainless steel springs, SUJ ball bearings, and SUS XM7 stainless steel cap screws are used to assemble the Rapfix II.
Not only does using A5056 in the Rapfix II make it even stronger than the Rapfix I, but this also shaved 174g off the weight of the Rapfix II ! And then you have a finished Rapfix II ...
So as you can see, an enormous amount of precision, care and work goes into making every Works Bell Rapfix II Quick Release.
SAFETY STANDARDS AND TESTING
In addition, The Works Bell Rapfix II meets the safety standards set by ASEA (Auto Sports & Special Equipment Association) which is the Japanese equivalent of SEMA. Works Bell's products have been subjected to a huge number of safety tests, including the following:
* Material Hardness Test
* Material Tensile Test
* JASO C713 Static load bending test on steering wheel
* JASO C713 Static load torsion test on steering wheel
* JASO C713 Static load fatigue bending test on steering wheel
* JASO C713 Static load fatigue torsion test on steering wheel
Test methods for steering wheels including boss kits in Japan are defined by the public JASO standards and JIS Standards. For the Rapfix, high impact tests beyond what is normally met during accidents are conducted. So just like Rays Wheels developed their own safety standard for wheels that exceeds the normal Japanese standards, Works Bell test their products to standards above the Japanese safety standards requirements. Here is a photo of one of the test rigs which was used to put huge loads into a Rapfix II during the safety testing ...
And finite element analysis is also carried out ...
WHAT CAN GO WRONG WITH KNOCKOFFS ?
I was at Eastern Creek in Sydney a few weeks ago for the Drift Australia round, and a number of the teams out there have had big problems with copy and counterfeit quick releases. I saw two cars with copies on them which the detents that the balls lock into had elongated and worn on, which then puts play into the steering and is a huge safety problem. Here is a photo I took on Sunday at the Drift Australia event at Eastern Creek of a quick release that is not a genuine Works Bell product which the detents that the balls lock onto had worn and elongated on. When the detents on the copies and counterfeits elongate and wear, the quick release no longer locks properly onto the steering column with the correct tolerances, the tolerances are then all wrong, and you end up with play in the steering ...
This happens because a number of the companies making copies (particularly in Taiwan and China) either:
* (a) don't understand the metallurgy required to make quick releases with proper durability and materials, and the required heat treating, or
* (b) because they choose lower grades of materials than what the genuine Works Bell ones use, either because of ignorance or to make the copies more cheaply to make more profit on them. One of the drift teams at Eastern Creek told me on Saturday that the copy they bought does not automatically lock onto the steering column like it should, so they need to manually lock the locking collar into place. That introduces human error into the equation - forget to manually lock a copy and there's a massively increased chance of an accident. Additionally one of the drift teams at Eastern Creek told me on Saturday that they were using a copy quick release, and at Oran Park the copy broke, and the wheel came off in the drivers hands at full speed, mid-corner !
The fact is that when products are designed and engineered, the drawing and design of the product is intricately linked with the grades of materials used to make the part. You simply can't take a drawing or design of a part that was designed to be made in a particular grade of material, and replace that material with some other grade. The same thing applies to heat treating - lower standards of heat treating cannot be substituted for the heat treating standard specified by the designer or engineer of the parts. If the engineer designing a part is told that the part is going to be made in lower grades of metals, or with lower standards of heat treating, then the design of the part MUST be changed to have the required strength. The materials specification and the design are two sides of the same coin - they go together to form the whole. Quite simply, any parts design is designed specifically with a link to particular grades of metals, and to particular grades or heat treating, and that link should NEVER be broken. And right there lies one of the huge fundamental problems with fakes, copies and knock offs - any quick release that is manufactured using the wrong grades of metals, the wrong standards of heat treating (if the fake, copy or knockoff is heat treated at all), and the wrong manufacturing techniques simply results in a part that is NOT within the manufacturing and safety standards that the original designer, inventor or engineer designed the part for.
Source: tunersgroup.com
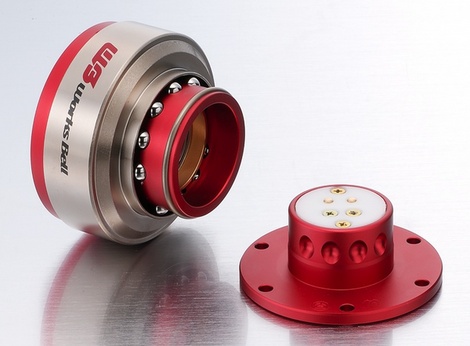
HOW THE GENUINE WORKS BELL RAPFIX II IS MANUFACTURED
It is not widely known, but Works Bell actually invented the Ball Lock Quick Release Locking System as seen in the Works Bell Rapfix II (and unfortunately also seen in numerous copies). Works Bell also holds the patent on this system. If you go to the press release on their website you will see comments from the CEO of Works Bell, Mr. Masato Miyashita on this point. It reads ..."CEO of Works Bell, Mr. Masato Miyashita said of the new business relationship with The Tuners Group ..."Works Bell has been manufacturing and selling steering hubs since 1971 and we have provided the steering hubs for a lot of Japanese manufacturers and companies. We developed the 12 Hole PCD steering hub which can be used both for Momo steering wheels and Nardi steering wheels in 1977. Furthermore, we also took the patent for this product. From then on, we have never failed in technology, quality and durability of our products. We are the number one manufacturer in Japan today. We have also received some patents for our other products and we research, develop and innovate on new products every day. We developed and received the patent on the Quick Release (Rapfix Ball Lock System) in 2001. We have produced and sold 30,000 Quick Release Rapfix systems to date. " The Works Bell Rapfix II Plug and Socket start out as billets of high strength A5056 alloy.This high strength A5056 Alloy is then heat treated to H34 standard which increases the yield strength of the metal by 60%, to approach that of Duralumin, widely known as a super strong material. Works Bell don't stop there though ...This high strength and heat treated A5056 Alloy is then cold die forged. Die forging is the same process used in the manufacturer of ultra high grade alloy wheels and is mentioned in our tech article about forging vs casting vs machining. Here are some diagrams of a metal part (shown in red) being made using open die forging ...
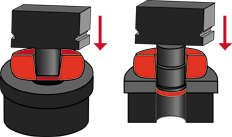
This die forging process process produces a forged blank that is close to the final shape of the Rapfix II. The die forging makes the metal ever more dense, and aligns the grain structure matrix with the forging flow lines. Here is a diagram of that process ...
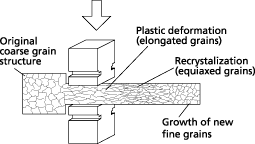
Forging aligns the grains of the metal like this ...
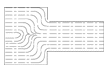
Here's a close up photo of the grain structure of a Rapfix after forging. The red lines show the flow of the grain structure after forging.
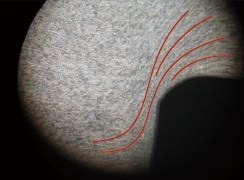
Here is a photo of the two main parts of a Rapfix II after forging and before machining
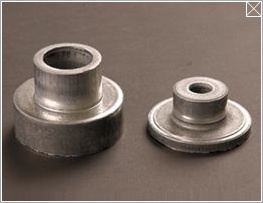
Next is the machining. Only now is the machining done, and because the grain structure is already aligned with the shape of the part via the cold die forging, the machining does not "cut across" the grain structure like the example shown in our tech article about machining non-forged metals.
The main body of the Rapfix is machined ...
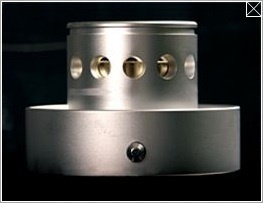
Next an Alumite oxide film is caused to form on the surface of the aluminium and stainless steel by soaking the parts in an electrolytic liquid solution and changing the temperature to produce a surface with superior corrosion and wear properties.This produces a hard alumite oxide film, that is harder than steel. Alumite performs beautifully on the exterior while reducing any wear from use ...
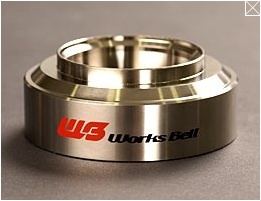
On the black version of the Rapfix II, Works Bell use a special treatment called hard almite to effect a black sleeve ...
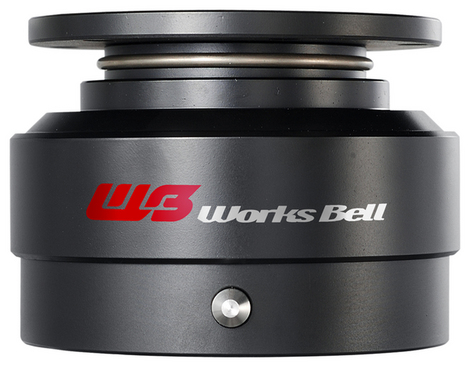
On the Rapfix II the inside sleeve where the socket and plug slide is then treated with a special teflon coating to make it much more difficult to scratch the anodizing ...
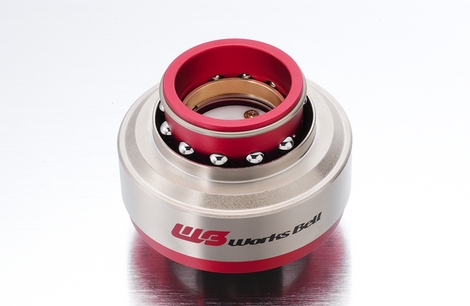
So now the Rapfix II is ready for assembly ... As you can imagine, Works Bell don't scrimp on quality here either. SUS304 stainless steel springs, SUJ ball bearings, and SUS XM7 stainless steel cap screws are used to assemble the Rapfix II.
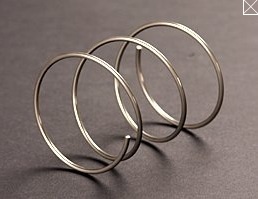
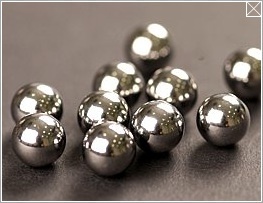
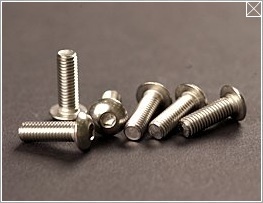
Not only does using A5056 in the Rapfix II make it even stronger than the Rapfix I, but this also shaved 174g off the weight of the Rapfix II ! And then you have a finished Rapfix II ...
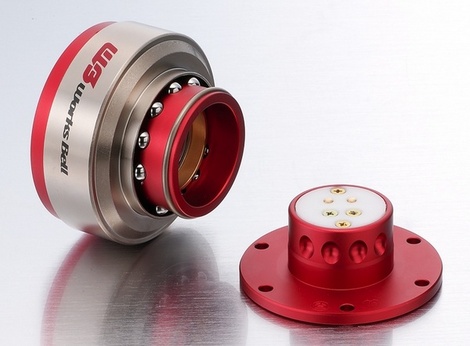
So as you can see, an enormous amount of precision, care and work goes into making every Works Bell Rapfix II Quick Release.
SAFETY STANDARDS AND TESTING
In addition, The Works Bell Rapfix II meets the safety standards set by ASEA (Auto Sports & Special Equipment Association) which is the Japanese equivalent of SEMA. Works Bell's products have been subjected to a huge number of safety tests, including the following:
* Material Hardness Test
* Material Tensile Test
* JASO C713 Static load bending test on steering wheel
* JASO C713 Static load torsion test on steering wheel
* JASO C713 Static load fatigue bending test on steering wheel
* JASO C713 Static load fatigue torsion test on steering wheel
Test methods for steering wheels including boss kits in Japan are defined by the public JASO standards and JIS Standards. For the Rapfix, high impact tests beyond what is normally met during accidents are conducted. So just like Rays Wheels developed their own safety standard for wheels that exceeds the normal Japanese standards, Works Bell test their products to standards above the Japanese safety standards requirements. Here is a photo of one of the test rigs which was used to put huge loads into a Rapfix II during the safety testing ...
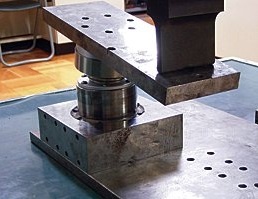
And finite element analysis is also carried out ...
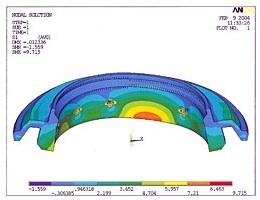
WHAT CAN GO WRONG WITH KNOCKOFFS ?
I was at Eastern Creek in Sydney a few weeks ago for the Drift Australia round, and a number of the teams out there have had big problems with copy and counterfeit quick releases. I saw two cars with copies on them which the detents that the balls lock into had elongated and worn on, which then puts play into the steering and is a huge safety problem. Here is a photo I took on Sunday at the Drift Australia event at Eastern Creek of a quick release that is not a genuine Works Bell product which the detents that the balls lock onto had worn and elongated on. When the detents on the copies and counterfeits elongate and wear, the quick release no longer locks properly onto the steering column with the correct tolerances, the tolerances are then all wrong, and you end up with play in the steering ...

This happens because a number of the companies making copies (particularly in Taiwan and China) either:
* (a) don't understand the metallurgy required to make quick releases with proper durability and materials, and the required heat treating, or
* (b) because they choose lower grades of materials than what the genuine Works Bell ones use, either because of ignorance or to make the copies more cheaply to make more profit on them. One of the drift teams at Eastern Creek told me on Saturday that the copy they bought does not automatically lock onto the steering column like it should, so they need to manually lock the locking collar into place. That introduces human error into the equation - forget to manually lock a copy and there's a massively increased chance of an accident. Additionally one of the drift teams at Eastern Creek told me on Saturday that they were using a copy quick release, and at Oran Park the copy broke, and the wheel came off in the drivers hands at full speed, mid-corner !
The fact is that when products are designed and engineered, the drawing and design of the product is intricately linked with the grades of materials used to make the part. You simply can't take a drawing or design of a part that was designed to be made in a particular grade of material, and replace that material with some other grade. The same thing applies to heat treating - lower standards of heat treating cannot be substituted for the heat treating standard specified by the designer or engineer of the parts. If the engineer designing a part is told that the part is going to be made in lower grades of metals, or with lower standards of heat treating, then the design of the part MUST be changed to have the required strength. The materials specification and the design are two sides of the same coin - they go together to form the whole. Quite simply, any parts design is designed specifically with a link to particular grades of metals, and to particular grades or heat treating, and that link should NEVER be broken. And right there lies one of the huge fundamental problems with fakes, copies and knock offs - any quick release that is manufactured using the wrong grades of metals, the wrong standards of heat treating (if the fake, copy or knockoff is heat treated at all), and the wrong manufacturing techniques simply results in a part that is NOT within the manufacturing and safety standards that the original designer, inventor or engineer designed the part for.
Source: tunersgroup.com