A lot of cars use brake torque vectoring. Heck, I just tracked an AWD Ford Flex and it was actively braking the inside front and rear wheels to minimize understeer. I didn't know a run-of-the-mill Flex had this function and was actually really impressed at how well it mitigated the understeer and helped turn the car. While it still eventually settled on a final understeer balance, entering corners and mid-corner, its programming of braking various wheels did help the car turn...
McLaren's 12C and 650 rely on hit heavily to brake the inside rear wheel to help turn the car when entering corners, as well as they get away with using NO LIMITED SLIP DIFF (an open diff) by using the brakes on the inside rear wheel to limit slip and distribute torque evenly (or more on the outer wheel) when putting power down.
Yes having individual electric motors can open a whole new level of potential for making a car go through a corner - as well as understeer mitigation! BUT as you start having active suspension, active diffs, active torque vectoring, and electric motors; it's a TALL order to get all the programs to work together in sync, feel natural, and contribute to the overall performance of the car. Remember how long the 918 took to develop and the hurdles they had to overcome? The NSX 2.0 has a ton of techology which could make it really good, or very disconnected, unnatural, and outright bad. It all depends on the engineers' execution. Like i said before, even McLaren is behind the ball to Ferrari with integrating their systems and they are some pretty smart people over there...
You can read my review on the McLaren 12C, and this systems integration issue here: (click the image)
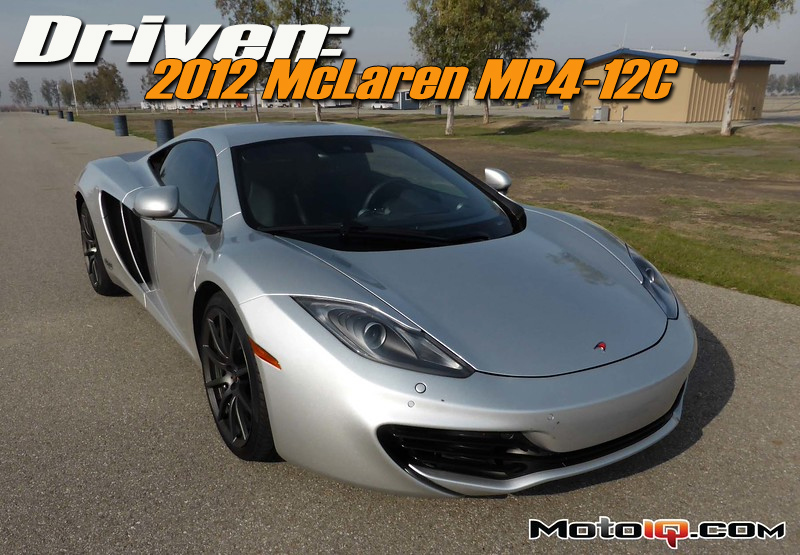
McLaren's 12C and 650 rely on hit heavily to brake the inside rear wheel to help turn the car when entering corners, as well as they get away with using NO LIMITED SLIP DIFF (an open diff) by using the brakes on the inside rear wheel to limit slip and distribute torque evenly (or more on the outer wheel) when putting power down.
Yes having individual electric motors can open a whole new level of potential for making a car go through a corner - as well as understeer mitigation! BUT as you start having active suspension, active diffs, active torque vectoring, and electric motors; it's a TALL order to get all the programs to work together in sync, feel natural, and contribute to the overall performance of the car. Remember how long the 918 took to develop and the hurdles they had to overcome? The NSX 2.0 has a ton of techology which could make it really good, or very disconnected, unnatural, and outright bad. It all depends on the engineers' execution. Like i said before, even McLaren is behind the ball to Ferrari with integrating their systems and they are some pretty smart people over there...
You can read my review on the McLaren 12C, and this systems integration issue here: (click the image)
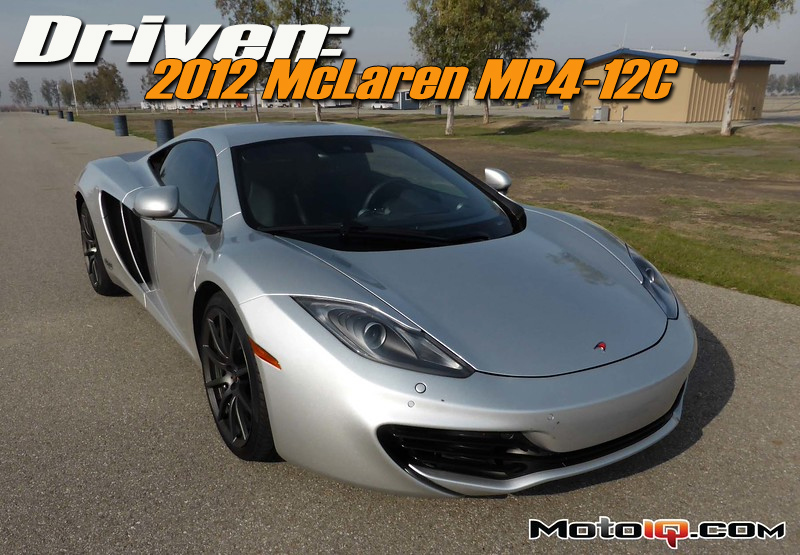