Transmission Swap pt2
Give it up for Daayyyy 2.
Finished the clutch pedal switch harness. I learned my lesson this time and used a 2P weatherpack instead of 2x 1P connectors. Black is to a factory ground, blue is to the cruise control unit wire on C425, white is supposed to be the clutch signal to the ECU but the reality is a bit more complicated and I haven't figured out the proper connection just yet.
To get more access to C425 (shift console switch, 12P connector) I went ahead and took out the A/T shifter assembly. 4 or 5 bolts and it lifts out. Take bolts off first then you can get access to take the cotter pin out from the bottom of the shifter.
Here's what it looks like with just the A/T shifter base still in.
Base removed. Plenty of room for activities.
A/T neutral safety switch jumper. I ended up just cutting off the connector on the old shifter and soldered the wires together. They're quite thick, like 10ga or something. Heat shrunk the end and now there's a permanent jumper to allow the engine to start.
C425 harness finished, much more simple since most of the old wires are no longer used. I could've made a disconnect for the clutch switch to cruise control input but the harness is short enough already. The blue wire goes into the factory BLU/ORG wire to the cruise control cancel input. I'll know if I have the wrong NO/NC switch if I can only activate cruise control with the clutch pedal depressed, lol.
The black jumper ties the GND pin to the Drive signal to always send Drive to the ECU(s). The FancyCraft blog here (https://fancy-craft.firebaseapp.com/NSX/report/at-mt/report4.htm) is confusing on this point since it shows a switch between Park and Drive since apparently "idling rises and it is not stable" according to Google Translate. I assume the idle map is different in Park vs. Drive but since 95% of the time when you're idling, you're in traffic and in Drive. We'll see, my money is that it'll be fine.
Here's the final patch harness for C161 next to the ECU. It's mostly red wires to the same old wires since there's only two pins I need to mess with.
One new green wire to lead into the ECU neutral switch input from my C499 patch harness. There's one other missing pin not included with the factory A/T harnesses, which is a PNK wire for the ECU clutch switch signal input.
Here's the end of my clutch switch wire to the ECU. There's no female pin on the ECU connector (top row, 3rd from left), so I'd need to find a terminal to add the pin myself. They look smaller than the HD-090 connector terminals I've been using so I need to do more research to find the right kind. Even the FancyCraft author doesn't really know what this input is for, presumably it's to tell the ECU not to use VTEC in neutral/with the clutch disengaged. The car should run regardless.
Some final installed harness pictures. Here's C161 again. That was a lot of crimping...
Here's C499 from before. Bit bulky with the new wires but the bulkhead panels should fit fine.
C425 harness installed. Connected the YLW wire from here to the backup lights on C499.
And finally, the clutch switch connectors. I did some adjustment of the switch with a multimeter to verify where the signal changed based on pedal position. That about does it for the wiring.
For a little underbody work, to fully remove the A/T shift cable I removed the cable cover and pin holding the other end of the cable on the transmission.
Hanger and rubber gasket for the A/T cables. Remove both and the cable pulls out from the back with the other two underbody brackets removed.
Cable removed.
Time to put stuff on. The new shifter base is a modification by Wayne of the stock A/T bracket. With some new tapped holes and the two top spacers, the bracket can be re-used for the manual shifter bracket.
Even OEM brackets sometimes don't fit perfectly. I needed to drill out the 4 bolt holes one size larger to line up right with the factory mount locations. Only a difference of 1-2mm in the end.
New base installed.
Assembling the shifter parts onto the Type-R shift stalk. No instructions for this so it took a little while to put the puzzle pieces together. The exploded parts diagrams for the shifter are clear enough to figure out how to put this all together. New Honda urea grease on all moving parts.
New shifter bushing snapped into place on the ball stud. There's this microscopic little cushion ball that goes in a hole on the bushing, and is only held in when you slide the shifter piece into the bracket holder. I used some grease to hold the ball in the bushing. So small you can barely see it installed here.
Shifter bracket assembled and ready to drop in. The blue block is the Cedar Ridge short shifter mod.
Shift cable connected to the Cedar Ridge short shifter and stalk.
Bracket fully installed with the parking brake back in.
View from the bottom with the shift & select cables installed. Not really any instructions for putting all this in but easy enough to figure out as you go. Now I can sit on the floorboard and pretend I'm a race car driver.
I used pretty much all new bolts & self lock nuts, bushings, grease, etc. Seems to shift just fine, there will probably be more adjusting to do once I connect the other ends of the cables.
That's most of the interior work done, mainly just some adjustments to make and reinstalling the steering column & seats. I'm gonna leave that for later in case I need to get to something inside.
Today my goal is getting the automatic transmission dropped out. We'll see, I've not messed with most of those bolts yet so it'll be a learning experience. As long as I don't separate the ball joints then it should go fine. I also have the big boy axle puller which I'm sure will need to be used. More updates to come.
Give it up for Daayyyy 2.
Finished the clutch pedal switch harness. I learned my lesson this time and used a 2P weatherpack instead of 2x 1P connectors. Black is to a factory ground, blue is to the cruise control unit wire on C425, white is supposed to be the clutch signal to the ECU but the reality is a bit more complicated and I haven't figured out the proper connection just yet.

To get more access to C425 (shift console switch, 12P connector) I went ahead and took out the A/T shifter assembly. 4 or 5 bolts and it lifts out. Take bolts off first then you can get access to take the cotter pin out from the bottom of the shifter.

Here's what it looks like with just the A/T shifter base still in.

Base removed. Plenty of room for activities.

A/T neutral safety switch jumper. I ended up just cutting off the connector on the old shifter and soldered the wires together. They're quite thick, like 10ga or something. Heat shrunk the end and now there's a permanent jumper to allow the engine to start.

C425 harness finished, much more simple since most of the old wires are no longer used. I could've made a disconnect for the clutch switch to cruise control input but the harness is short enough already. The blue wire goes into the factory BLU/ORG wire to the cruise control cancel input. I'll know if I have the wrong NO/NC switch if I can only activate cruise control with the clutch pedal depressed, lol.
The black jumper ties the GND pin to the Drive signal to always send Drive to the ECU(s). The FancyCraft blog here (https://fancy-craft.firebaseapp.com/NSX/report/at-mt/report4.htm) is confusing on this point since it shows a switch between Park and Drive since apparently "idling rises and it is not stable" according to Google Translate. I assume the idle map is different in Park vs. Drive but since 95% of the time when you're idling, you're in traffic and in Drive. We'll see, my money is that it'll be fine.

Here's the final patch harness for C161 next to the ECU. It's mostly red wires to the same old wires since there's only two pins I need to mess with.
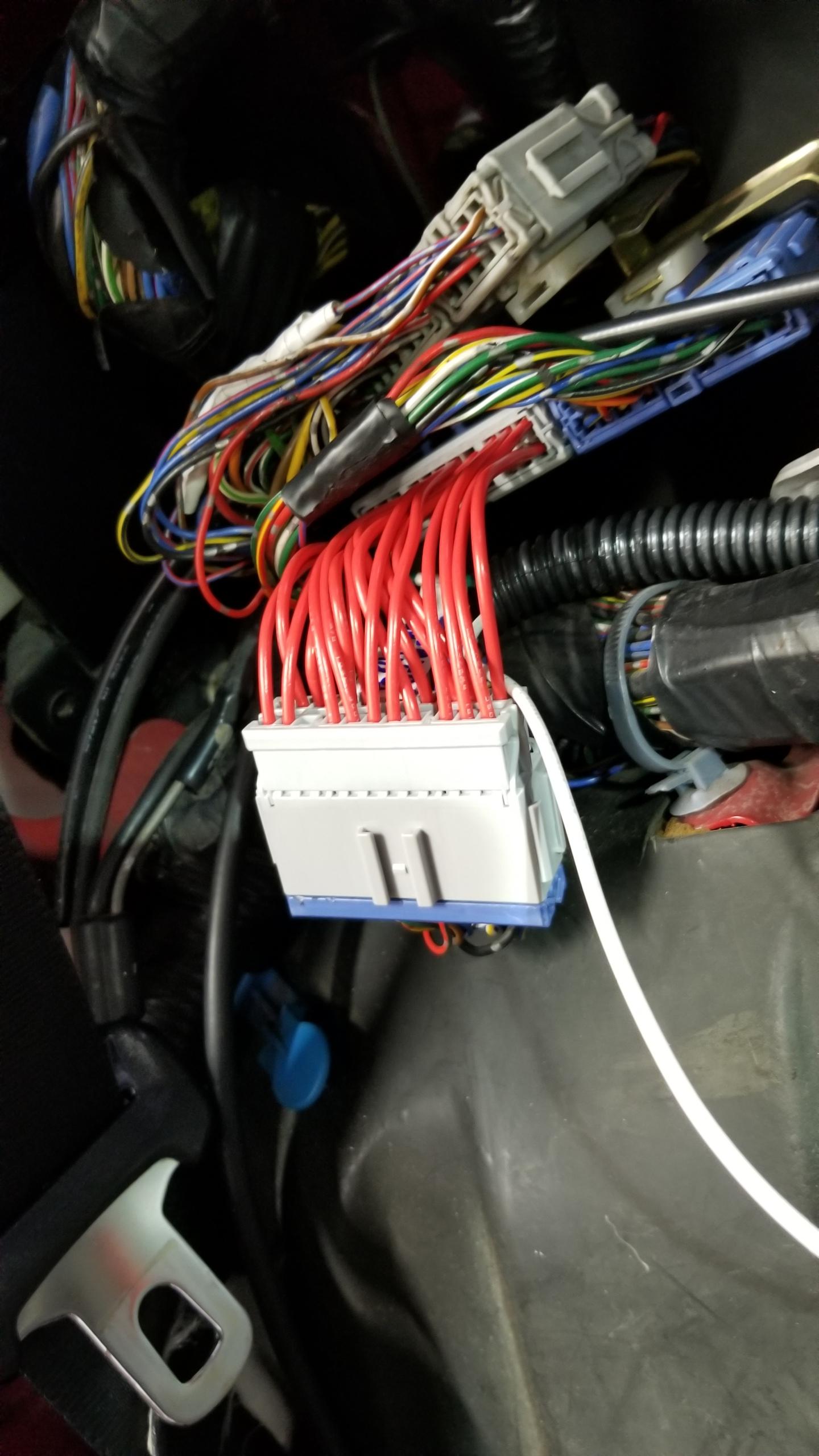
One new green wire to lead into the ECU neutral switch input from my C499 patch harness. There's one other missing pin not included with the factory A/T harnesses, which is a PNK wire for the ECU clutch switch signal input.
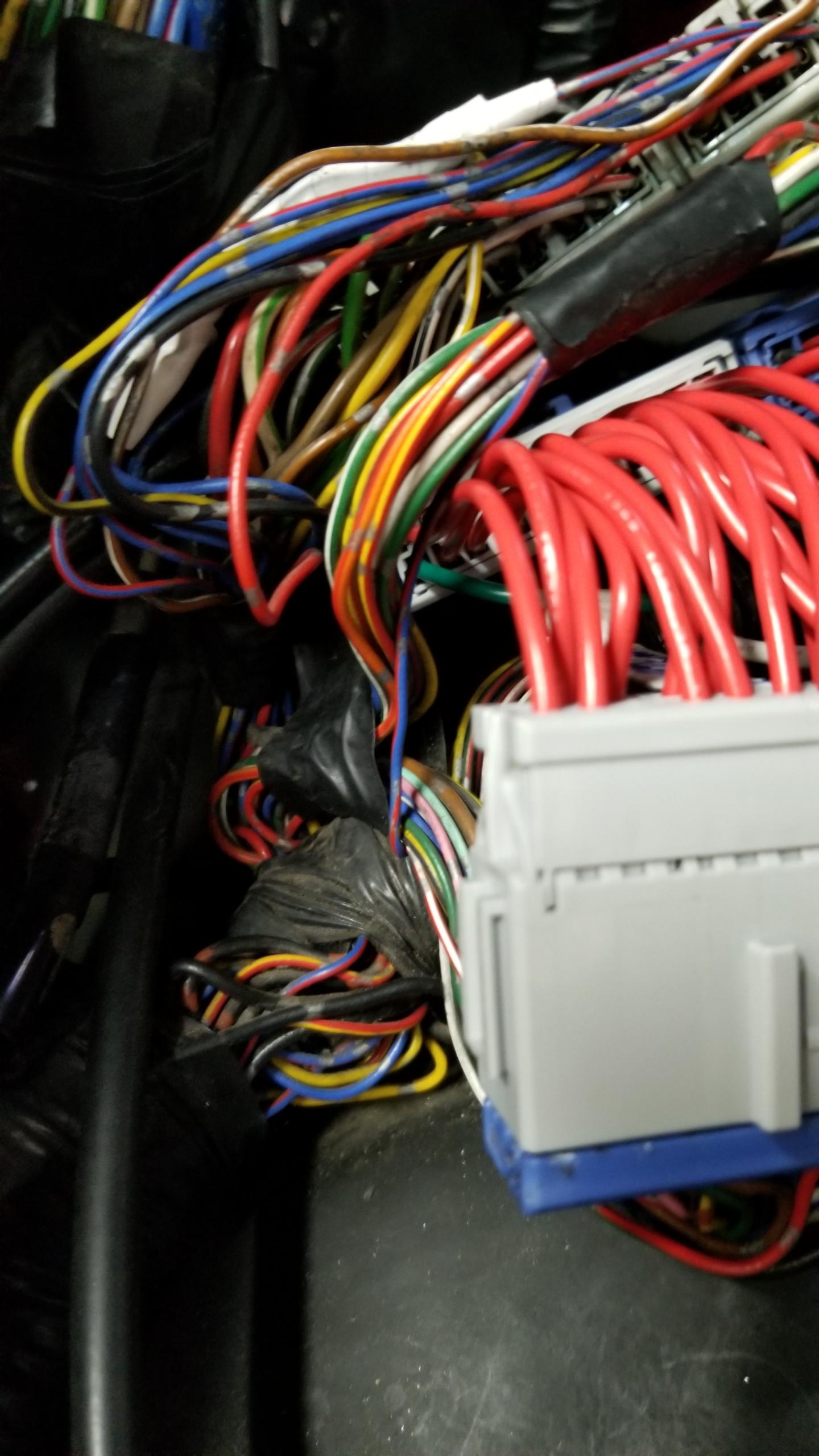
Here's the end of my clutch switch wire to the ECU. There's no female pin on the ECU connector (top row, 3rd from left), so I'd need to find a terminal to add the pin myself. They look smaller than the HD-090 connector terminals I've been using so I need to do more research to find the right kind. Even the FancyCraft author doesn't really know what this input is for, presumably it's to tell the ECU not to use VTEC in neutral/with the clutch disengaged. The car should run regardless.
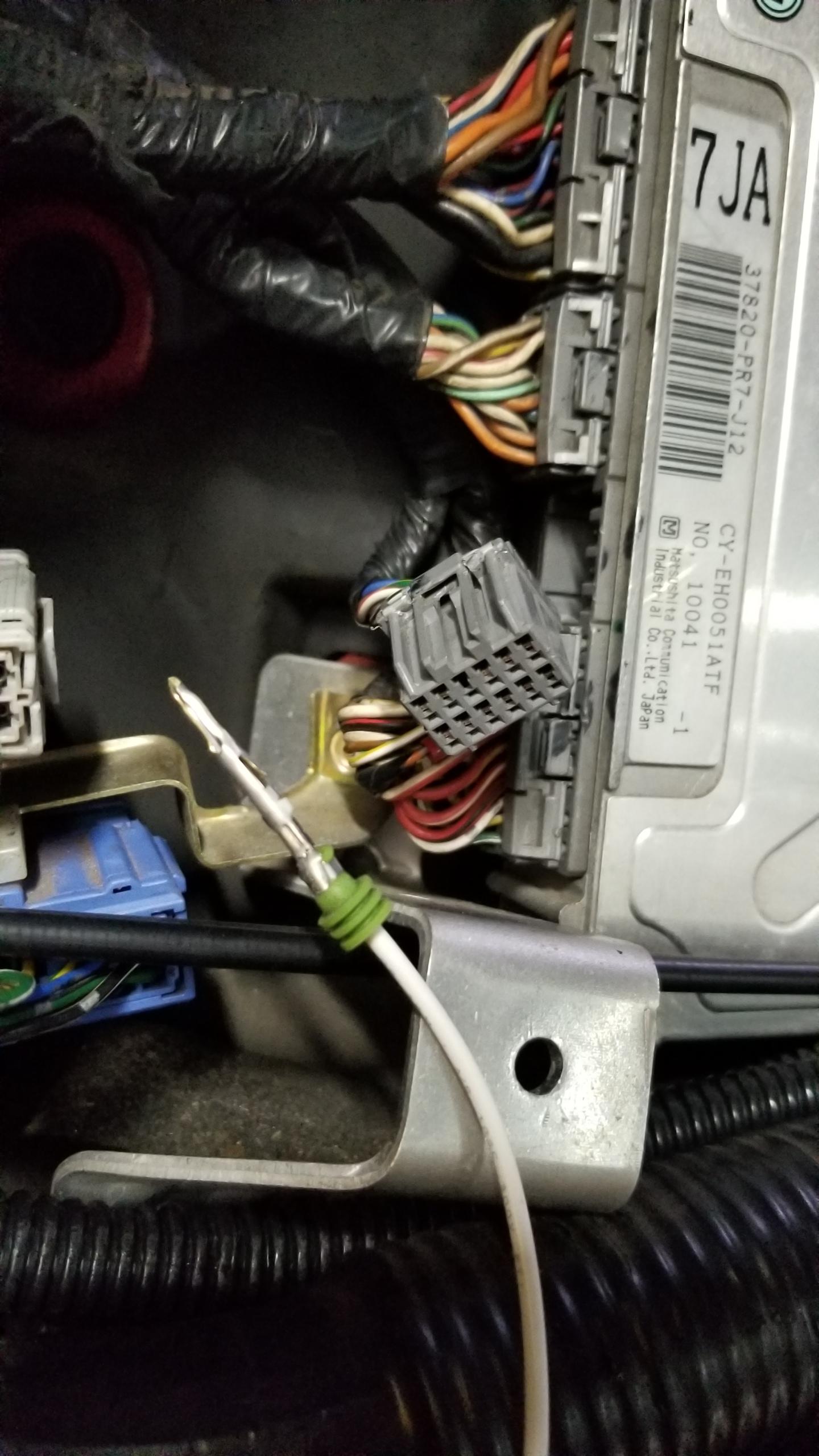
Some final installed harness pictures. Here's C161 again. That was a lot of crimping...

Here's C499 from before. Bit bulky with the new wires but the bulkhead panels should fit fine.

C425 harness installed. Connected the YLW wire from here to the backup lights on C499.

And finally, the clutch switch connectors. I did some adjustment of the switch with a multimeter to verify where the signal changed based on pedal position. That about does it for the wiring.

For a little underbody work, to fully remove the A/T shift cable I removed the cable cover and pin holding the other end of the cable on the transmission.

Hanger and rubber gasket for the A/T cables. Remove both and the cable pulls out from the back with the other two underbody brackets removed.

Cable removed.

Time to put stuff on. The new shifter base is a modification by Wayne of the stock A/T bracket. With some new tapped holes and the two top spacers, the bracket can be re-used for the manual shifter bracket.

Even OEM brackets sometimes don't fit perfectly. I needed to drill out the 4 bolt holes one size larger to line up right with the factory mount locations. Only a difference of 1-2mm in the end.

New base installed.

Assembling the shifter parts onto the Type-R shift stalk. No instructions for this so it took a little while to put the puzzle pieces together. The exploded parts diagrams for the shifter are clear enough to figure out how to put this all together. New Honda urea grease on all moving parts.

New shifter bushing snapped into place on the ball stud. There's this microscopic little cushion ball that goes in a hole on the bushing, and is only held in when you slide the shifter piece into the bracket holder. I used some grease to hold the ball in the bushing. So small you can barely see it installed here.

Shifter bracket assembled and ready to drop in. The blue block is the Cedar Ridge short shifter mod.

Shift cable connected to the Cedar Ridge short shifter and stalk.

Bracket fully installed with the parking brake back in.

View from the bottom with the shift & select cables installed. Not really any instructions for putting all this in but easy enough to figure out as you go. Now I can sit on the floorboard and pretend I'm a race car driver.
I used pretty much all new bolts & self lock nuts, bushings, grease, etc. Seems to shift just fine, there will probably be more adjusting to do once I connect the other ends of the cables.

That's most of the interior work done, mainly just some adjustments to make and reinstalling the steering column & seats. I'm gonna leave that for later in case I need to get to something inside.
Today my goal is getting the automatic transmission dropped out. We'll see, I've not messed with most of those bolts yet so it'll be a learning experience. As long as I don't separate the ball joints then it should go fine. I also have the big boy axle puller which I'm sure will need to be used. More updates to come.